The grapple for warehousing with nearshoring
29 Jan 24
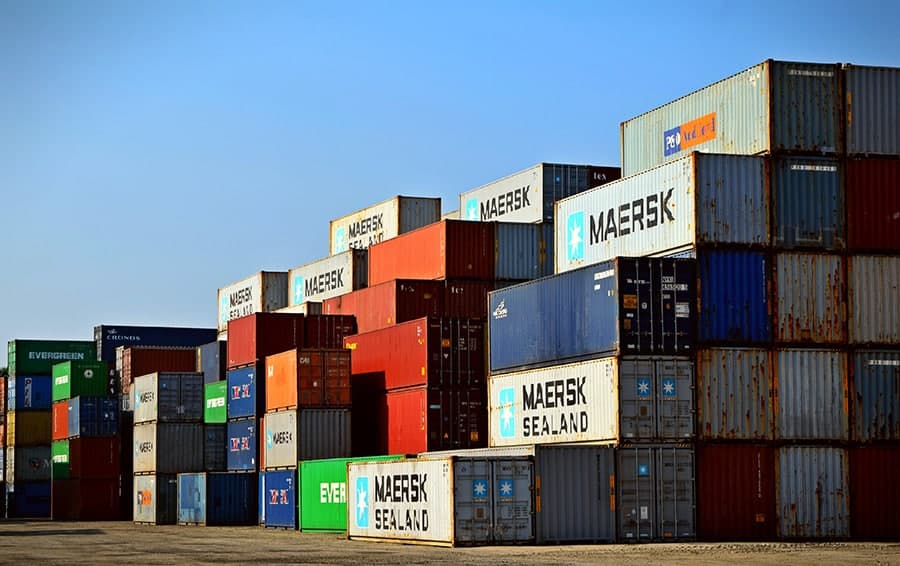
Geopolitical uncertainties, and evolving trends are some of the catalysts for the significant shift we’re seeing in how businesses develop their supply chain strategies. Increasingly, we’re seeing organisations pivot from global supply chains which rely on a single global source to nearshoring, where local hubs manufacture, store and / or distribute goods closer to the main consumer market.
The driving force behind this re-evaluation of the supply chain is the pursuit of greater supply chain resilience. However, while the trend towards regionalisation does enhance an organisation’s ability to adapt better to unforeseen challenges and changes in demand, moving from global to regional operations is not a simple task.
Why is nearshoring challenging?
Companies face challenges both old and new which need to be carefully considered and planned for to ensure the strategy has the most positive impact for the business.
One of the key challenges organisations will face is how it changes the flow of goods in the supply chain. If you’re importing finished goods, then local storage and distribution centres need to be relatively close to where consumer demand is for efficient and sustainable logistics. But if manufacturing is being brought closer to home, then you’ll need these warehousing spaces to be located nearby with safety stock readily available, such as spare car parts, for example.
For those looking to bring their supply chains closer to home in Europe, they will see that competition for warehouse space is hotting up, especially for larger tenants, and we expect this to only increase. We’re already experiencing a shortage of warehousing space due to the increasing trend for nearshoring, also driven by the acceleration of e-commerce in markets such as France and the UK, and emerging sectors including battery manufacturing growing across continental Europe.
While it used to be very easy for tenants such as retailers and 3PLs to snap up warehousing space, this is no longer the case. And this lack of surplus means tenants can be at the mercy of what’s available in the market and the landlords that provision them – from the quality of the asset to raising the rents ad-hoc.
Understanding your warehousing needs
The warehouse is absolutely critical to nearshoring success. We’re seeing in the market that some tenants are already taking premises in Europe as far ahead as 2027 to secure their future with a regionalised supply chain. With competition high, organisations must act with purpose when looking for these sought-after spaces. But, equally, consideration for what’s right for their operations must be made. Here are six factors:
wp:list
wp:list-item
Owning vs. leasing:
First, organisations consider what type of relationship they want with their warehousing space. Do they build and run/lease it for themselves if they have the capital to do so? Or as we often see, take out a new tenancy or enter a sale-leaseback agreement, for example, which puts the responsibility of the infrastructure on the landlord.
/wp:list-item
/wp:list
Land location:
There are several factors that impact location selection for warehousing. These can include whether it has the required resources available for the facility such as water and power i.e. for an energy demanding site, whether it has accessible transport connections such as main highways if it is a key logistics hub, and the distance from suppliers or consumers to minimise transportation costs and fuel.
Size and scalability:
If companies choose to enter a lease, they must consider the long-term viability. For example, do they lock into a space further to their requirements and sublet it until they’re ready to scale? Do they lease a space that’s right for ‘now’ with the understanding that when they require more space, they will need to look for a secondary warehouse (which is likely miles away)? It’s important to have at least a 10-year view on the operational roadmap to ensure you’re not undermining chances for efficient growth.
Fit for future technologies:
Emerging technologies are changing the game in logistics and warehousing operations, such as using automation to pick orders or using electric vehicles for last-mile deliveries; helping to drive greater operational and sustainable efficiencies. This will only increase in the future and organisations should plan for how technologies will impact the space required.
Sustainable credentials:
Decarbonisation will continue to ramp up and companies must prioritise greening their warehousing operations as part of decarbonising supply chains in the future. Organisations should look out for spaces with ‘green’ fixtures such as energy-saving LED lights, energy-efficient white thermoplastic polyolefin (TPO) roofs that reduce energy expense compared to traditional dark-coloured roofing materials, solar panels, and more.
Compliant with local legislations:
Companies scaling to new markets must understand the nuances between regional legislation on warehousing requirements or risk compliance breaches. For example, in the UK, steel-framed structures dominate warehouses, while France mandates concrete structures due to fire safety regulations. These structural differences impact the entire supply chain, from automation to approval processes.
Strategic planning for regionalised supply chains
While challenges do exist, nearshoring also brings several overall opportunities. More control, better vendor management, improved sustainability credentials and more streamlined communication can all be achieved, but only when plans are strategic and thorough.
The decision to move to a regionalised supply chain needs to align with business objectives and the needs of customers. Crucially, given the ongoing property shortage, there is the need to pre-plan, not just based on the business in its current state, but also accounting for growth over the coming decades. Keeping this in mind will help businesses to not suddenly come up against warehouse shortage issues, but rather to anticipate and acquire what will be needed ahead of time.